Executive summary
The aerospace industry is one of the most regulated sectors in the world, with strict requirements for certifications of all products used in manufacturing aircraft.
About 90 percent of the quality certification documentation in the sector is still handled in paper format. Manufacturers, distributors, and suppliers must issue, handle and archive thousands of documents daily, which is time-consuming and costly for the companies.
The German-Estonian company TraCert is trying to change the situation and allow aerospace companies and manufacturers in other industries to digitalize their certification paperwork easily.
The Cert-Trace platform developed by Helmes allows all parties to the supply chain to upload and store certificate-of-conformity documentation on a secure encrypted cloud. The documents can be accessed by scanning a unique QR code corresponding to each document. The integrity of documents is ensured by blockchain technology, which makes it impossible to modify a document without leaving a trace in the database.
The solution allows companies in the aerospace industry to drastically reduce the manual work involved in handling quality certification documents and cut related costs. It is estimated that the aerospace industry could save €80 million annually in Europe alone by digitizing quality certification documentation. Furthermore, digital documentation also improves the companies’ data analytics capabilities and opens up further possibilities for innovation.
Read from the case study how the Cert-Trace platform supports the aerospace industry in implementing the digital certificate-of-conformity (e-CoC) certification process and the benefits it brings to the companies using it.
Meet the customer
TraCert is a German-Estonian company set on solving one of the challenges facing the aerospace industry today – the digitalization of quality certification documentation. The team members have a decades-long experience in the sector, from distribution companies and standardization organizations, and recognized the huge potential of replacing paperwork with digital documentation.
When a digital data exchange format for quality certification documents in the aerospace industry was introduced in Europe in 2020, the company partnered with Helmes to build a technical solution that would allow companies across the supply chain easily go paperless.
The challenge
The aerospace industry is one of the most regulated sectors in the world, with strict requirements for certifications of all products used in manufacturing aircraft. All aspects involving different supply chain members need full certification, from raw materials to manufacturing processes to the final product, and the documentation needs to be stored long-term.
Approximately 90 percent of this documentation is currently handled on paper, while the amount of documentation per single bolt can amount to dozens of pages.
Suppliers, distributors, and manufacturers must issue, verify and archive massive documents daily, which is time-consuming and costly.
It is estimated that the aerospace industry could save €80 million annually in Europe alone by digitizing quality certification documentation. However, the implementation of digital documentation first needed a legislative change. It only became possible after DIN SPEC 9012 – a digital data exchange format for quality certification documents in the aerospace sector – was adopted in 2020.
The solution: The Cert-Trace platform for digital certification
Cert-Trace is a web-based platform that allows companies in the aerospace industry to replace paperwork with digital documents easily. Manufacturers and suppliers in other industries can also use the platform.
When a new quality certification document is issued, the employee can upload it to a secure, encrypted cloud instead of printing it out. The system generates a unique QR corresponding to the document.
When a manufacturer ships a package, they no longer have to include the paper documentation but can attach a QR code. The recipient can access the documentation by scanning the QR code, checking and approving it, or requesting changes.
The immutability of the documents is guaranteed by Quantum Ledger Database technology. The system creates a unique hash code for each document stored in a transparent, immutable, and cryptographically verifiable transaction log. Whenever a document is modified, the system automatically creates a new record in the database, which allows for easy verification of the integrity of documents.
The system can be used as a standalone application or integrated with SAP or other ERP systems for maximum automation. Many European aerospace companies and organizations have already adopted the system, which can be easily scaled when the number of users grows.
Benefits
The Cert-Trace platform offers various benefits to its users:
Time and cost savings
The system reduces manual work and increases operational efficiency for all parties to the supply chain. For instance, upon delivery, a shop floor employee can scan a QR code and verify and approve one digital document instead of manually stamping every page of a lengthy paper document.
Immutability of certificates
The integrity of certificates is ensured by blockchain technology, which makes it impossible to modify the documents without leaving a trace in the database.
Easy access
Any document can be effortlessly located amongst a vast collection of documents by scanning a QR code. The documents can be retrieved instantly after production. For instance, a customs official can receive and check the documentation before the physical shipment arrives.
Integration with other IT systems
Cert-Trace can be used as a standalone system or easily integrated with SAP or any other ERP system for maximum benefits.
Potential for innovation
The platform improves the companies’ data analytics capability and opens up further possibilities for innovation, including those involving AI and machine learning.
Reduced carbon footprint
Switching to the digital format is an environmentally friendly approach that contributes to reducing the carbon footprint of the whole industry.
Team and work process
The project team included a technical lead, a project lead, developers, an analyst, a tester and designer from Helmes, and a product owner from TraCert.
- Before embarking on collaboration, we held a joint workshop in Estonia, followed by a preliminary analysis phase and drawing up the development roadmap.
- After the client accepted our proposal, we moved on to an in-depth analysis of business and technical needs.
- Next, we entered the active development phase while following our usual agile approach, developing and testing the solution hand in hand.
The whole development process took approximately six months. The solution went live in 2021 and is currently used by clients in Europe and the U.S.
As the client’s team was located in Germany and Helmes’ team in Estonia, our daily collaboration mainly took place online, relying on scheduled weekly meetings and ad-hoc communication. The team also met once a year on-site during the project.
Helmes as an innovation partner
Helmes is also the first Estonian IT company to become an official supplier to Airbus.
If you are looking for a development partner with experience in the aviation and manufacturing sectors, we’d be happy to hear from you.
Get in touch
Get in touch
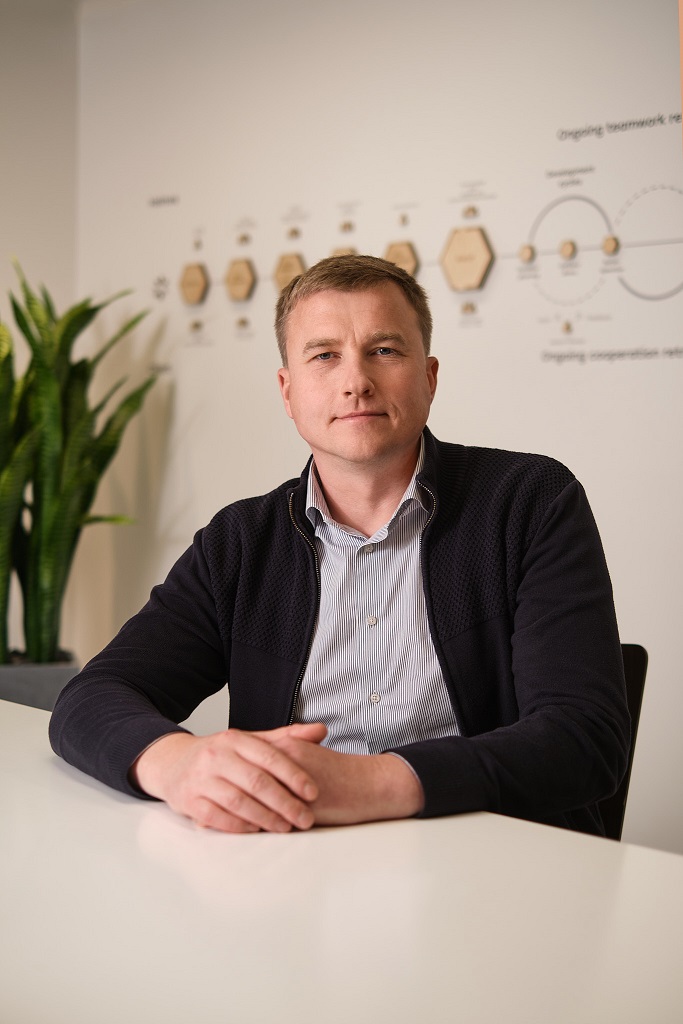