Airbus is a global leader in the aerospace industry and the world’s largest aircraft manufacturer. In 2021, Helmes became the first Estonian IT company to become an official supplier to Airbus, providing its aircraft-manufacturing subsidiary Airbus Commercial with an IT system that makes one stage of its production process significantly more effective.
Aviation is a highly regulated sector, and the number of standards related to aircraft design, manufacturing, and the supply chain has been increasing steadily.
As a result, Airbus saw a need for a fully customized project management platform that would simplify the daily work of its internal standardization team.
Helmes was tasked with developing the system, and in June 2022, the Airbus New Standardization Portal (NESPA) was rolled out in the Airbus headquarters in Toulouse, France. Today it is an official Airbus application used by its employees worldwide. The development process took less than six months from start to finish.
NESPA is a project management platform fully customized for the Airbus internal standard team. The web-based portal provides a comprehensive overview of all ongoing and planned standardization projects, their progress, and allocated budget. The application allows team members to easily track tasks required to implement a specific standard and simplifies reporting and budget planning.
Improving the user experience for the team members was a key focus. Thanks to NESPA, the Airbus standardization team can perform their everyday tasks faster and with less manual work involved in the process.
This case study outlines the benefits of a fully customized project management application for a global manufacturing company, describes the process of largely remote collaboration between Airbus and Helmes, and the keys to our successful partnership that allowed us to deliver the project without a hitch on a very tight schedule.
Meet the customer
Airbus is a leader in designing, manufacturing, and delivering aerospace products, services, and solutions to customers worldwide. The company operates in the commercial aircraft, helicopters, defense, and space sectors and constantly innovates for efficient and technologically advanced solutions.
Airbus has over 125,000 employees worldwide and business operations on six continents.
The challenge
A key aspect of manufacturing airliners is the implementation of new technical standards. Aviation is one of the most highly regulated sectors in the world. An aircraft manufacturer must comply with rigorous standards developed by industry organizations regarding the design and manufacturing processes and sourcing parts from suppliers.
Airbus needed a digital tool to help its internal standardization organization implement new and updated standards more efficiently.
The company envisioned a platform fully customized to their needs that would:
- gather all documentation on a central platform and provide a comprehensive overview of all standardization projects;
- visualize resource allocation and facilitate budget planning;
- ramp up the user experience and cut the manual work for the standardization team.
Because the standardization projects are planned in yearly cycles, it was crucial to roll out the new system by July 2022. Otherwise, the launch would have been postponed by a year.
The solution – A fully customized project management application
Helmes was tasked with developing the platform, and after five months, the Airbus New Standardization Portal (NESPA) was launched in June 2022.
NESPA is a project management application custom-developed for the Airbus internal standard organization, and the web-based portal can be accessed by authorized users anywhere in the world. Used daily by several hundred employees, the cloud-based system can be easily scaled as the number of users increases.
The system has various roles with different levels of access. Logged-in users can see on their dashboard all the projects they are involved in and project data: the project leader, requested budget, site, working group, etc. As the project progresses, it moves through various stages from pending to approved to completed, so there is a comprehensive overview of the progress and associated costs at any moment.
Users can easily track the tasks they need to perform to implement a specific standard (for instance, attending working group meetings or traveling). As all the data is stored on the platform, it is no longer necessary to juggle between different programs to find the necessary information (while it is naturally possible to export data if needed).
The system considerably simplifies statistics and budget management. Thanks to a comprehensive overview of the projects and in-built reports, it is easy to track the cost of implementing different standards and plan the budget for coming years.
The team and daily collaboration
The 10-member project team included the following members:
- a technical lead and a project lead,
- developers,
- an analyst,
- a tester,
- a designer,
- and product leads and the project sponsor from Airbus.
With Airbus team members located in France and Helmes team members in Estonia, our collaboration mainly took place online, relying on regular weekly meetings and ad-hoc communication when needed.
We held a two-hour team meeting each week with different agenda items but the same structure. First, we analyzed the development needs and next steps, discussed any open issues, and finished with a demo of the completed parts of the system.
The work process
Brainstorming → Prototype → User interviews → Analysis → Development & Testing → Launch
Before starting the collaboration, we held a two-day workshop in Tallinn with Helmes and Airbus team members, where we mapped the development needs and brainstormed possible solutions. At the end of the workshop, we proposed the preliminary technical solution and development timeline and budget, followed by a detailed proposal over the following weeks.
After our proposal, we designed a prototype that the product owner used for end-user interviews inside Airbus. After implementing the changes derived from the user feedback, we moved on to a month-long analysis phase. We analyzed both business and technical needs and drew up a development roadmap, after which the actual development could start.
Over the next three months, development and testing took place in parallel, and our engineers presented the completed parts of the system at our weekly joint meetings. Throughout the development process, we moved nimbly and could incorporate ideas suggested by the client.
Rolling out the new system
In June 2022, NESPA was launched in the Airbus headquarters in Toulouse, where the largest group of the portal’s users are located. Today, NESPA is an official Airbus application used by its employees worldwide. The next major step, the portal’s rollout in all German production units, is scheduled as the next users.
The June launch date was critical as new standardization projects for the following year were to be approved in July. Successful delivery meant that all projects for the year 2023 could be processed in the new portal.
The rollout took place on time and went smoothly, as we had prepared detailed documentation and self-guides for onboarding the team to the new application.
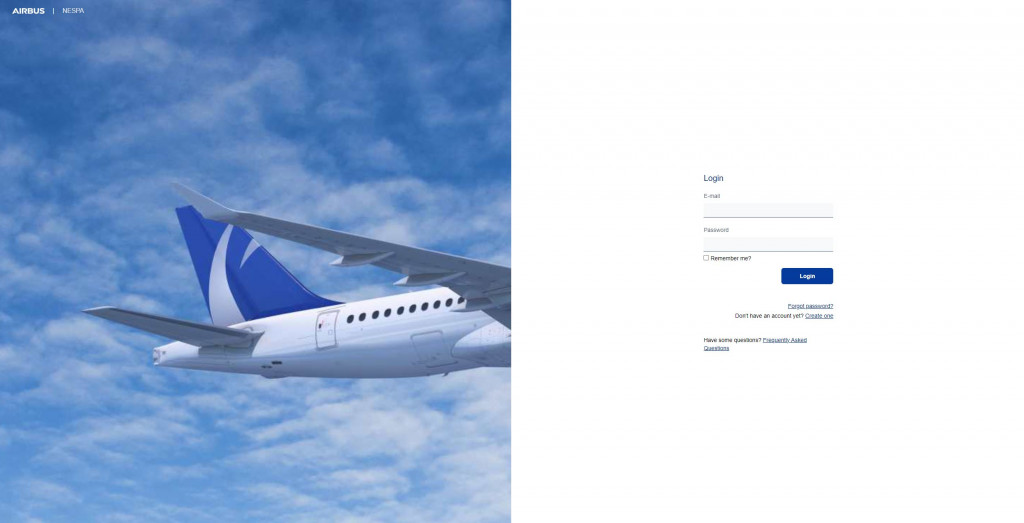
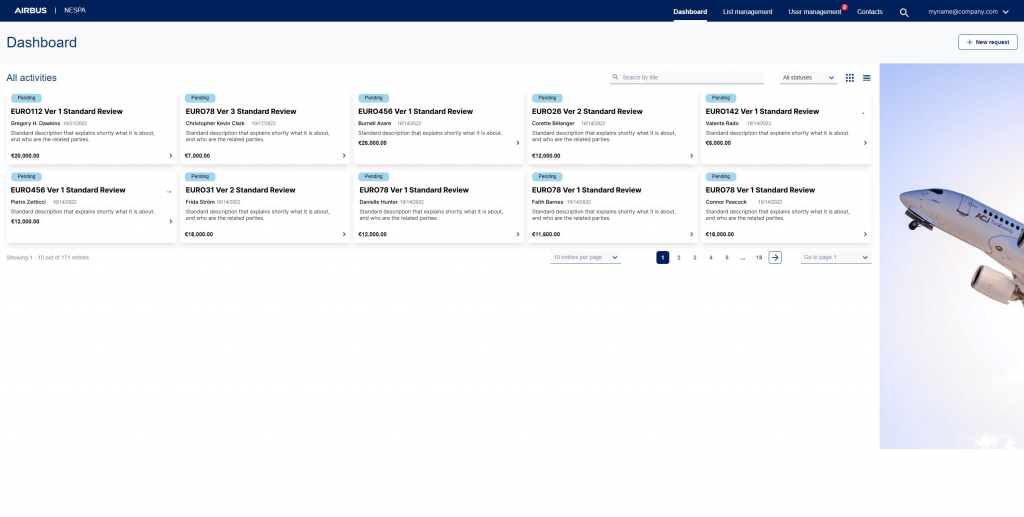
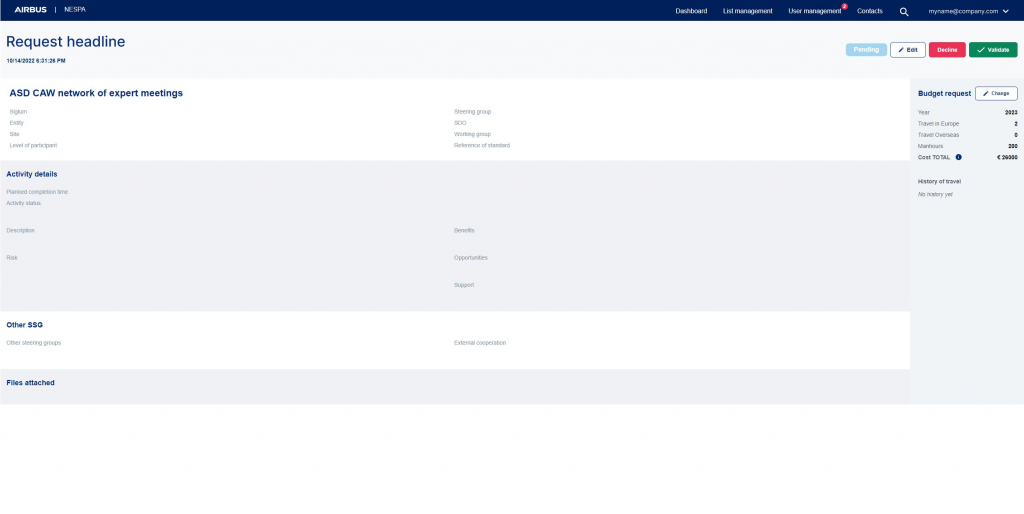
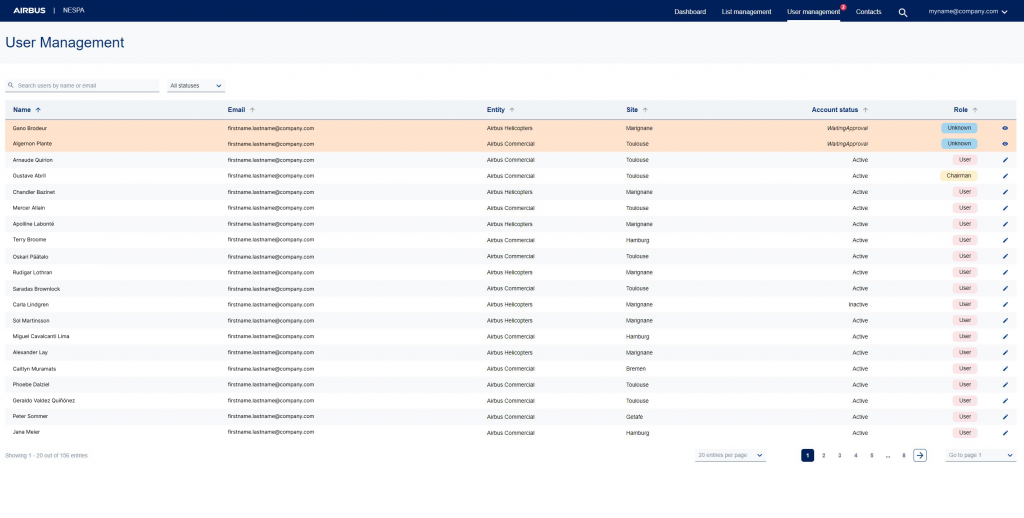
Helmes as an innovation partner
Trust and involvement are key to any successful collaboration. It is a real honor for Helmes to develop software for the world’s leading aircraft manufacturer and contribute to their mission towards a better-connected world.
Despite the vast differences in our company sizes, we have felt like a valued partner for Airbus since the beginning of the process. Thanks to the high level of trust and involvement from the client, we could complete the project without any setbacks on a tight schedule and deliver a solution used daily by Airbus employees worldwide in less than half a year.
We see Helmes as one of the main players in digital innovation due to their great experience in the field. I can say that Helmes was a perfect partner for that project. It is also appreciated that they are small enough to be fast and big enough to cover our needs so that they can work both proactively and reactively, adapting to our needs.
Giovanni David, Airbus Corporate Affairs representative
Let’s get to work
If you are looking for a development partner with experience in the aviation and manufacturing sectors, we’d be happy to hear from you.
Get in touch
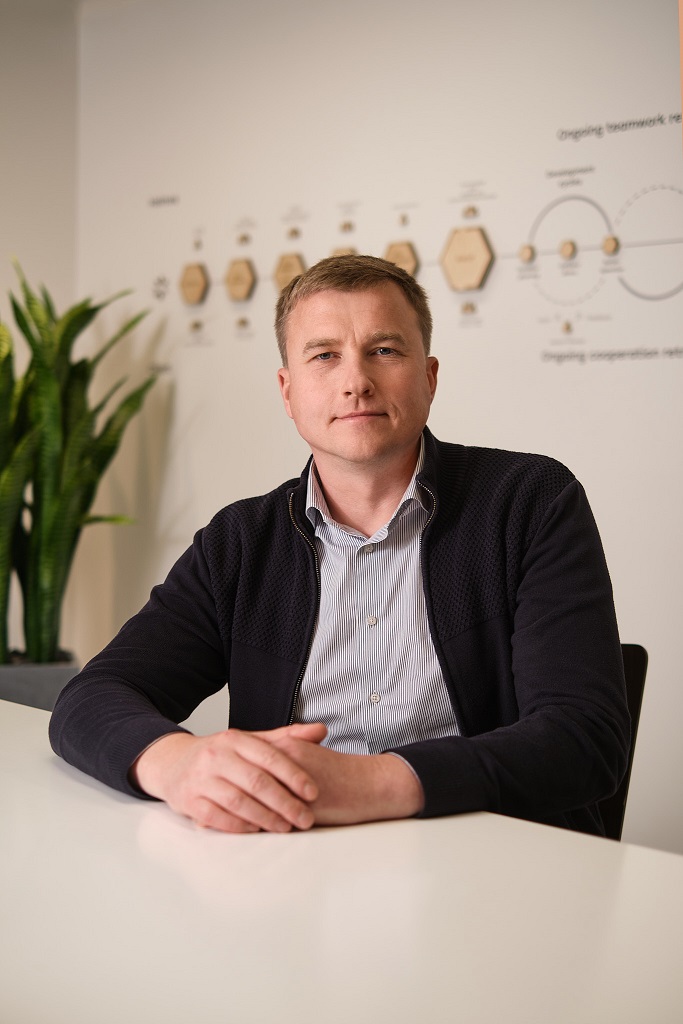