Find out how an innovative mindset of the Estonian Agricultural Research Centre and a well-designed digitalization process helped to develop laboratory software that delivers lab test results 30% faster.
What is the Estonian Agricultural Research Centre?
The Estonian Agricultural Research Centre (ARC) carries out many essential functions for the farm sector in Estonia.
One of the most critical departments of the ARC is its four different laboratories that provide testing services for farmers.
These labs analyze everything from viral infections on potato plants and vegetables to measuring seeds’ purity and moisture content to detect soil contaminants and pesticide residues.
While much of the ARC laboratories’ actual science and analysis is state-of-the-art, the information storage and sharing systems needed updating.
Helmes was selected to help bring the information and digital revolutions to their work processes.
Data inefficiency in research laboratories
The ARC laboratories were created at different times in different eras.
Since the labs mainly had developed and grown independently, there was no regularized information input and storage system.
This separate development process led to an ad hoc situation full of online spreadsheets, paper printing, and ink document signatures. Files were swapped from person to person on either paper or a flash drive when they needed to be shared.
The task of our Helmes team was to build a standardized system that would allow the Agricultural Research Centres’ five laboratories to communicate more efficiently.
Secondly, we had to utilize the advantages that digital communication technology provides organizations in their daily workload.
Listening to the lab workers
“My previous experience in biochemistry helped me to ask the right questions and analyze the answers” – Rene Väli (Lead Analyst)
Our team’s first step was simple – to listen – we hung around the labs, talking to the scientists and employees and observed how they worked. One of our analysts had worked in a laboratory environment before, so he quickly gained the trust of the workers.
Lab workers commented afterward that the Helmes team asked more questions than all the previous developers tasked to devise a solution. Lab workers loved that we focused on the small details that really mattered to them.
The contribution of laboratory staff can certainly not be underestimated. Their willingness to answer our questions and their patience in explaining various topics was crucial to the success of the project. Without the contribution of laboratories, the solution created would not have been as effective as it turned out to be.
Different labs with different data scales
The four Agricultural Research Centre laboratories took in many samples for analysis every year – 80,000 on average.
However, each laboratory was very different in scale and personnel. For example, one laboratory analyzed 50,000 soil samples each year.
At the same time, other labs take in a more modest number, between 1,000 and 5,000. One lab had two workers completing all the tasks.
In contrast, the largest had a staff in the dozens, with each technician focused on a very narrow field of analysis.
While working toward a common solution for these labs, the team took into account that the ARC was rebuilding its physical facilities. A new digital system can be obsolete if the change in facilities causes internal processes and logic to change.
Developing the business process model
Our next step was to map all the lab processes on a whiteboard.
Workers who have been doing their jobs for ages don’t remember all their actions to complete their tasks. A technician who takes a sample and develops an analysis might have eight links in a chain between receiving the sample and getting the data.
Then, the data might end up in a notebook that would later be transferred to a computer spreadsheet, namely Excel or the legacy laboratory software system. Only 5 percent of the legacy systems’ potential was being used. Documenting in Excel took between 30-60 minutes to complete!
All these steps were documented and put into the business process model (BPM).
“Storyboarding is the easiest way to imagine the future in a co-creating session.” – Mikk Tasa (Head of Design)
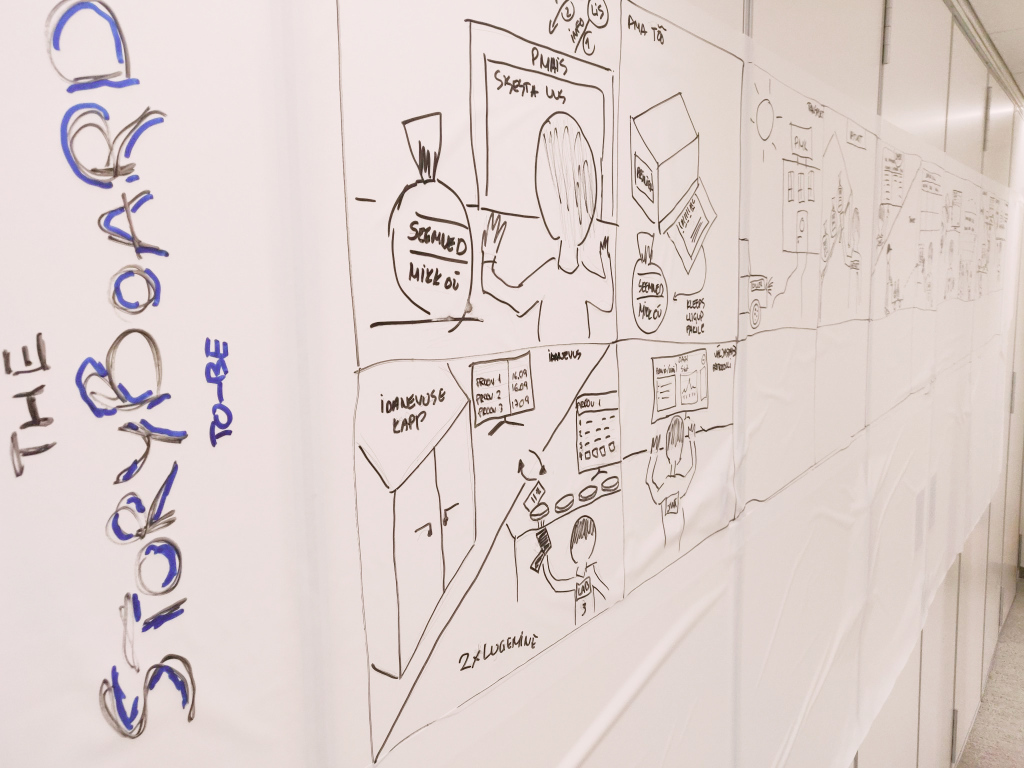
A service designer then joined the team in the development project. He asked questions like, “Why do you do certain things a certain way?” This form of questioning began a discovery process for the client to question their methods of working.
Our service designer made a diagram of a user experience journey. By mapping out the stages of daily work and the “pain points” the lab workers experienced (such as lost time and energy, or even emotional pain), it became apparent what the obstacles were in creating a newer, efficient way of working.
Those pain points illustrate the real problems, usually a duplication of information. Transferring data from one system to another would be an example, such as writing the same information repeatedly, first on paper and then to a computer file.
It turned out it took most of the laboratories’ day.
The Double Diamond process
In design thinking, one essential tool is the Double Diamond, developed in 2005 and used as a framework for innovation to tackle and transform how organizations develop and deliver their services.
You must discover what people do, research and define their problems, develop strategies, and provide solutions.
We held many workshops in the Helmes’ headquarters to figure out how people inside these labs work and think. At the same time, we needed to think about how the future system might work constantly.
Developing a prototype
Finally, Helmes’ team started working on a prototype, which had to be tested and validated. We asked the ARC employees to do their work in our newly developed system.
We recorded how users responded to the new laboratory software. Using our motion-sensor equipment, we observed how they navigate the system’s logic and layout and, most importantly, where they stumbled. Helmes could then refine its design process.
The development of a successful prototype was done with the valuable input of the laboratory staff. It is essential to point out that time must be set aside for testing. Fortunately, the lab staff was willing to invest time to benefit from changes made thanks to the thorough testing process.
We used a process called slicing. Instead of doing five laboratories separately and then monitoring the results, we focused on redesigning the processes in one lab.
After validating that the process works, labs can replicate when needed. We began operations with the most advanced lab first. Then worked our way to one that was still using pen and paper (our solution is eco-friendly, vastly reducing the need for both).
Every lab had to have new layers added, but the core logic was the same for all. The pre-analysis phase is now over, and ARC employees have also accepted the design. The detailed prototype is ready.
The project lasted a year and a half (from the first meeting to production), and the Helmes team working on the ARC project consisted of seven members:
- the team leader
- the architect and lead developer
- two other developers
- a system analyst
- a front-end developer
- a service and UI designer
The cooperation was a daily affair between the Ministry of Agriculture, ARC, and Helmes, with one of our team members frequently onsite or, if not, talking with lab technicians every day. Each week, the team had a meeting, discussing what would be achieved that week and communicated to ARC accordingly.
Redesign = streamlined data management
Why should chemists, who need to analyze samples, spend half their working day writing down numbers?
Why should workers waste their time writing notations on stickers placed on samples?
The end goal was to connect the chromatographs to the new system so that:
- workflow management was more efficient
- workflow management systems permitted the sharing of sample analysis
Helmes developed a tool where every lab can configure their analysis (the client has over 200 different ones) on every sample of soil, fruits, vegetables, etc. Most were previously done on paper or through a legacy system. Now the five individual labs can configure their analysis within their design.
The new system takes data from multiple laboratories.
After the system is fully integrated, each lab can configure its analysis by setting up its custom fields and rules to generate different data reports. Even better, labs could see which sample goes to which lab and appear on their customized dashboard so they can see the results and measure them.
All samples are easy to scan and load into the system. Samples will become easier to track, and recording the data will be more accurate than using pen and paper or the legacy system.
Critically, the lab technicians can work faster – sample analysis calculations are done automatically and not manually anymore.
With the new system employed at the ARC’s laboratories, its employees can focus on their primary responsibilities: getting much-needed data and analyzing Estonia’s entire agricultural community.
The first laboratory has been successfully digitized, the workflow and analysis settings of the following laboratories are in progress. The transfer of each laboratory to the system leads to changes in the work process, including changes in staff behavior and thinking.
When all laboratories have been digitized, the labs’ work will be 30% more efficient, and the quality and format of the results will be unified.
Thanks to the innovative mindset of the Estonian Agricultural Research Centre and Ministry of Rural Affairs, the Estonian agricultural sector gets the lab results at least 30 percent faster.
The laboratories, on the other hand, have easily scalable laboratory software that digitalizes the processes and enables greater effectiveness at work.
Get in touch
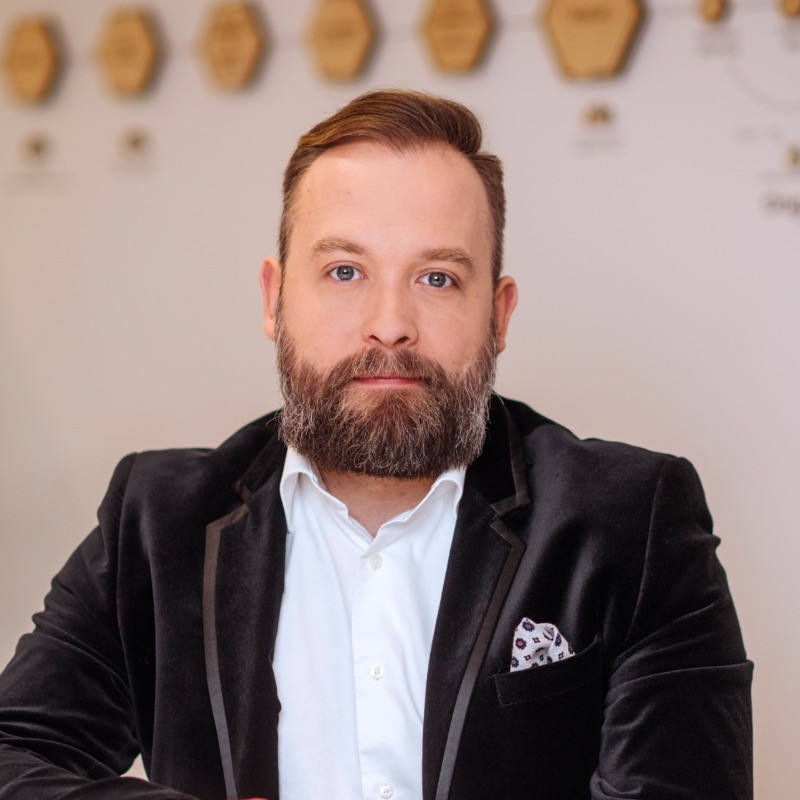